Ultrasonic Bonding Ensures Particle-Trapping Capability Of Panel Filters
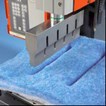
West Chester, PA - Sonobond Ultrasonics' bonding units continue to be the assembly equipment of choice for panel filter manufacturers striving to improve product quality and speed production. The machines use high frequency vibrations to create a continuous seal that encapsulates frames between
filter media, giving the filters added rigidity and effectiveness.
"With ultrasonic assembly, there are no stitch holes to compromise the integrity of the weld as you'd have with traditional sewing assembly methods," explains Janet Devine, president, Sonobond Ultrasonics. "Plus, there's no need for consumables, like thread. Ultrasonic assembly is a fast and efficient method that ensures the particle-trapping capabilities of filters."
Ultrasonic Assembly of Panel Filters
Panel filters are an important component of HVAC and dust collection systems, trapping unwanted particles between layers of nonwoven filter media as air enters and leaves. During the assembly process, frames, that add stability to the filters, are encapsulated between layers of nonwoven filter media. The center of the filter panel is often spot welded for extra rigidity.
In ultrasonic assembly, high-frequency vibrations are channeled to the nonwoven filter media as it passes between the horn and rotating pattern wheel of Sonobond's SeamMaster High Profile Bonder. The rapid heat buildup at the material contact point causes the material to melt, creating a strong continuous seal. The synthetic material is cut and sealed in just one pass, producing seams that are stronger, safer and more economical than those produced by other assembly methods. Sonobond's SureWeld 20 Ultrasonic PlungeBonder uses the same technology to spot weld the filter media in the center of the filter.
Material Viability for Ultrasonic Assembly
"The nonwovens used in panel filters are ideally suited for ultrasonic bonding because of their high synthetic content," says Devine. "Material must be at least 60 percent synthetic in order for it to be favorable for ultrasonics. Either way, we suggest that manufacturers submit their material for free testing in our applications lab."
In addition to panel filters, Sonobond's ultrasonic bonding equipment is used to assemble a wide variety of filtration applications, including industrial and commercial vacuum bags, oil absorbers, and automotive air filtration.
Sonobond Ultrasonic Bonders The SeamMaster High Profile Bonder is as easy to use as a conventional sewing machine, but four times faster, running at speeds up to 60 feet per minute. It's appropriate for hand-guided applications with tight tolerances or curves and works up to 10 times the speed of adhesive methods, making it exceptionally cost-effective. An optional speed-up kit can increase operation up to 120 feet per minute. The SureWeld 20 PlungeBonder is a versatile and rugged welding press with a heavy-duty power supply that ensures superior, repeatable performance. Both machines are available as stand-alone or modular units for integration into production lines.
A Leader in Ultrasonic Bonding Technology
Sonobond is a worldwide leader in the application of ultrasonic welding and bonding technology. In 1960 Sonobond, then known as Aeroprojects, received the first patent ever awarded for ultrasonic metal welding. During the intervening 47 years, Sonobond has earned an outstanding reputation for its pioneering work and quality-engineered products. Today, Sonobond manufactures a complete line of ultrasonic bonding and welding equipment for a wide variety of customers in the automotive, appliance, electrical, HVAC, aerospace, filtration, medical, and apparel industries.
SOURCE: Sonobond Ultrasonics'